During my Engineering Education in 2007-2011 Pakistan suffered from some of the worst power outages. The demand was much higher than the requirement of the people. This worsened during during the summer months. I remember spending countless days in the sweltering heat sweating and envying the abundance of solar energy that we had around us but no way to contain it.
​
My Bachelor Thesis was a group project where we made a prototype for a Solar Trough as a proof of concept. We designed it in CAD and then sourced all the materials locally to make it as cost effective as possible. While the trough wasn't functional. It still demonstrated that we can locally design and manufacture such projects.
​
​

After graduating in 2011, I was employed as a Design Engineer in AE Design Pakistan. AEDesign at that time was working on a project called Sundish, It was a parabolic dish with which concentrated solar energy to the focal point. My first project was doing a linkage study so that we don't have any clashes.

My most intense project with Sundish was designing and manufacturing a Solar Boiler for steam generation. Using the same energy that was used to drive a stirling engine before.
​
The first part of the project was finding the feasibility of the project, I contacted about 70 different textile mills in Pakistan to find out their requirements for Steam. Compiled them to find out their requirements. The steam quality required by most industries was 10 bar and 180℃ at 2-3 tph.
​
Next step was to make an analytical model. Siangsukone et al had made a similar model before for a mono-tube open cavity receiver as shown below.

I simplified the analytical model and programmed it in EES ( Engineering Equation Solver) to find out the output that we could get. It went to be something like that:
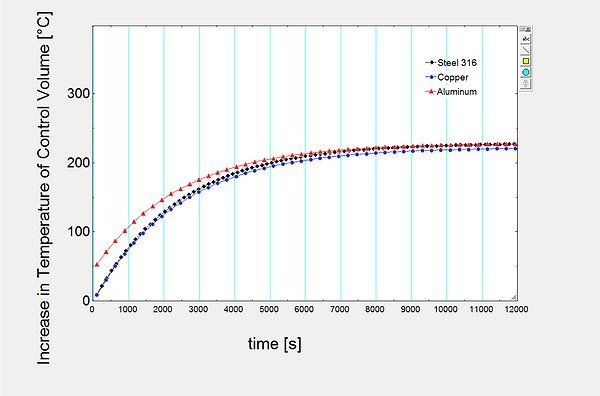
Note that the material that was chosen here was Stainless Steel, because of its high heat and corrosion resistance.
The next steps were to find out the Area of the receiver tubes and their optimum diameter. For the Area: Control Volume was plotted against the Total exposed area of the tube coil (Length of the tube x Outer diameter of the tube)

For the optimum radius there were a number of factors, firstly from below graph there is not much difference after a certain radius in the intake exergy. Secondly Stainless Steel tubing is only available in selected diameters. Keeping in mind these factors a suitable radius was chosen.
Below Graph by P.Bannister. (n.d.). Maximization of Exergy Gain in High Temperature Solar Thermal Receivers by Choice of Pipe Radius.

.
After finding out the length, radius and and the material of the tubes for optimum steam output, the next step was an optical analysis to find out the optimum geometry of the receiver so that maximum solar flux is utlized. for this purpose several geometries were modelled in Google Sketchup and then Analyses in SOLTRAC, one example is shown below.


The figure on the right shows the ray tracing for a cylindrical receiver , the figure on the left shows the flux distribution. The different colors show the intensity of the solar flux. The optimum heat flux is when there is a very gentle gradient without any localized hot spots.
The prototype was then made and tested. After passing the testing successfully it is now being commercialized by ZED Solar, the daughter company of AEDesign. For more information please visit the website.

The final Assembly mounted on the Sundish.